In manufacturing, harnessing the power of data analytics has become essential for driving efficiency and staying competitive. This blog delves into the impact of data on manufacturing processes, highlighting its pivotal role in achieving operational excellence.
From ancient methods of data management to cutting-edge machine learning technologies, we’ll explore how data analytics has evolved over time. Read as we uncover the foundations of process improvement, examine historical insights, and unveil the critical role data analytics plays in optimizing every aspect of manufacturing.
According to NewVantage Partners 3 in 5 organizations are using data analytics to drive business innovation. This statistic signifies that a substantial majority of forward-looking enterprises are no longer merely navigating the data landscape but actively leveraging it to chart new territories of innovation.
Foundations of Process Improvement in Manufacturing
In the world of manufacturing, building a strong foundation for process improvement is essential for sustained success. Think of it as the solid ground upon which a successful manufacturing operation stands.
Imagine three pillars: data analytics, root cause analysis, and the Kaizen philosophy. These aren’t just fancy terms; they’re powerful tools.
Data analytics is like a strategic guide, providing insights that help decision-makers optimize processes. It’s the compass pointing toward efficiency.
Root cause analysis is the detective work. It delves into core issues, ensuring that improvements aren’t just surface-level fixes but address the real challenges for long-term success.
Then there is Kaizen, a philosophy of continuous improvement. It’s about making small, meaningful progress regularly. This creates a culture where improvement isn’t a one-time event but a way of life.
By embracing and integrating these foundational elements, manufacturers create a roadmap for adaptability, efficiency, and a culture that’s always improving. It’s not just about doing things, but doing them better, smarter, and together.
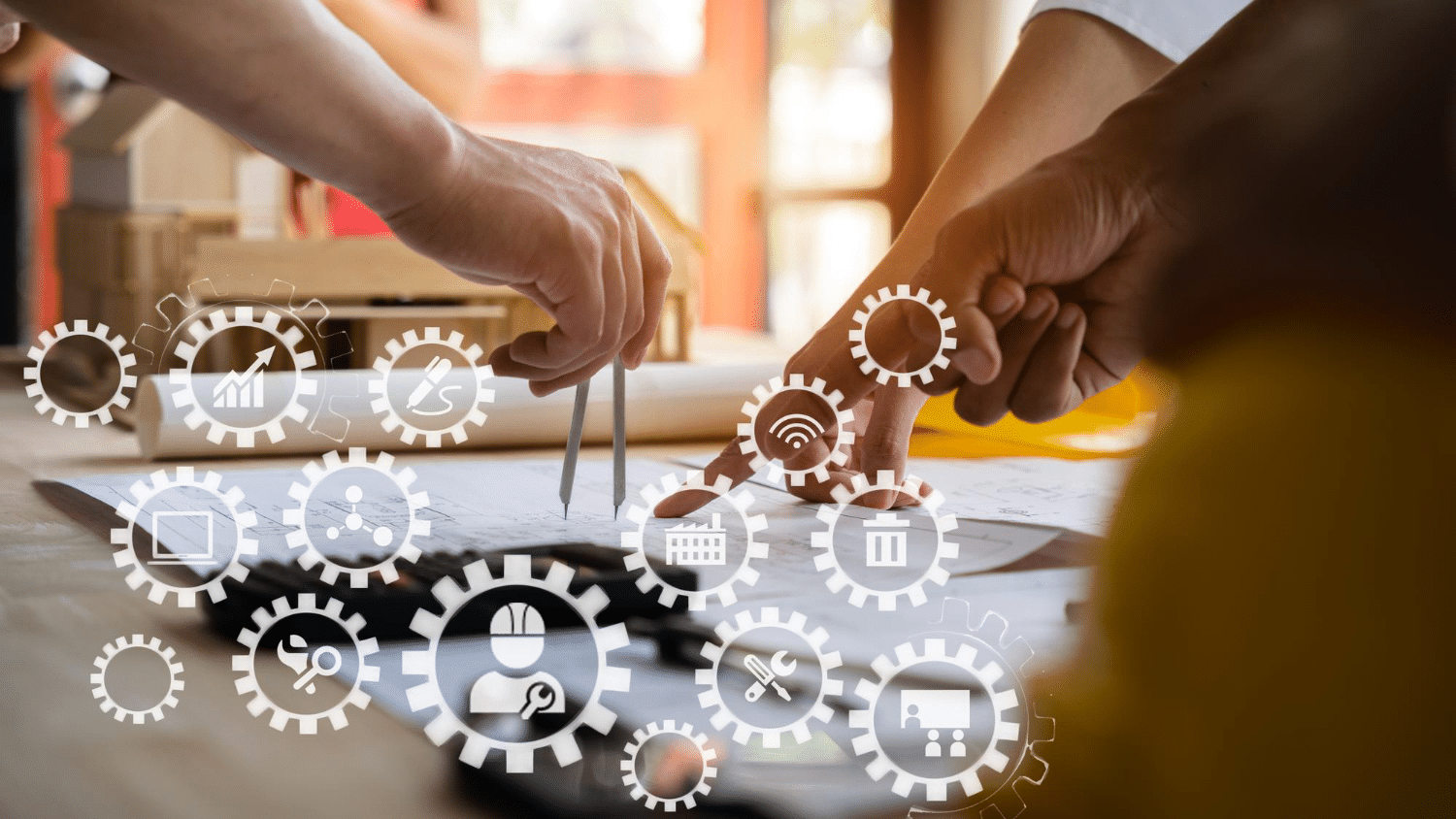
Data Analytics: Unraveling Insights Through Time
The concept of data analytics, while rapidly evolving in contemporary contexts, has ancient roots that span thousands of years. From Paleolithic tribes using notched bones for record-keeping to the intricate mechanisms of the ancient Greeks, humanity has engaged in primitive yet effective ways of managing information. As civilizations progressed, so did the methods of data analysis.
Ancient Roots of Data Analytics
In 18,000 BCE, the Ishango Bone, adorned with notches, showcased early data storage practices among Paleolithic tribes. The abacus in 2400 BCE Babylon marked a leap in calculations and data manipulation. The Antikythera Mechanism around 100-200 CE, possibly tracking Olympic Games and celestial events, demonstrated early mechanical computation.
Incorporating Statistics
The 17th century marked the beginning of statistical analysis, with John Graunt’s London experiment in 1663 aiming to predict the Plague. The term “business intelligence” was coined in 1865, and the Hollerith Tabulating Machine in 1880 streamlined the US Census Bureau’s data processing.
Modern Data Storage Concepts
The mid-20th century brought innovations like magnetic tape storage by Fritz Pfleumer in 1928. In 1944, librarian Fremont Rider foresaw the need for expanding library capacities. Large data centers, conceived in 1965, aimed to house vast amounts of data, while Edgar Codd’s relational database in 1970 laid the foundation for contemporary data services.
The Internet Era
The invention of the internet by Tim Berners-Lee in 1991 revolutionized data accessibility globally. The mid-1990s witnessed the emergence of NoSQL databases to manage internet-driven information flow. In 1997, Google search became a ubiquitous tool for internet data retrieval.
The Emergence of Big Data
In the 1990s, data mining uncovered patterns in extensive datasets. The term “big data” was officially introduced in 1999, coinciding with the emergence of the Internet of Things. Hadoop, an open-source framework for data storage and analysis, was created in 2005.
The Current Landscape
By 2008, worldwide servers processed over nine zettabytes of information, and by 2009, large companies were storing over 200 terabytes of data. The advent of Data Lakes in 2010 allowed raw data storage in large repositories. In 2014, mobile devices surpassed computers for digital data access. The years 2015 to 2020 witnessed a doubling of available datasets, accompanied by breakthroughs in AI, deep learning, and machine learning.
In the past few decades, data analytics has undergone a metamorphosis, shaping the modern landscape of technology and decision-making. The journey from ancient notches to contemporary machine learning is a testament to the enduring human quest to unravel insights from data.
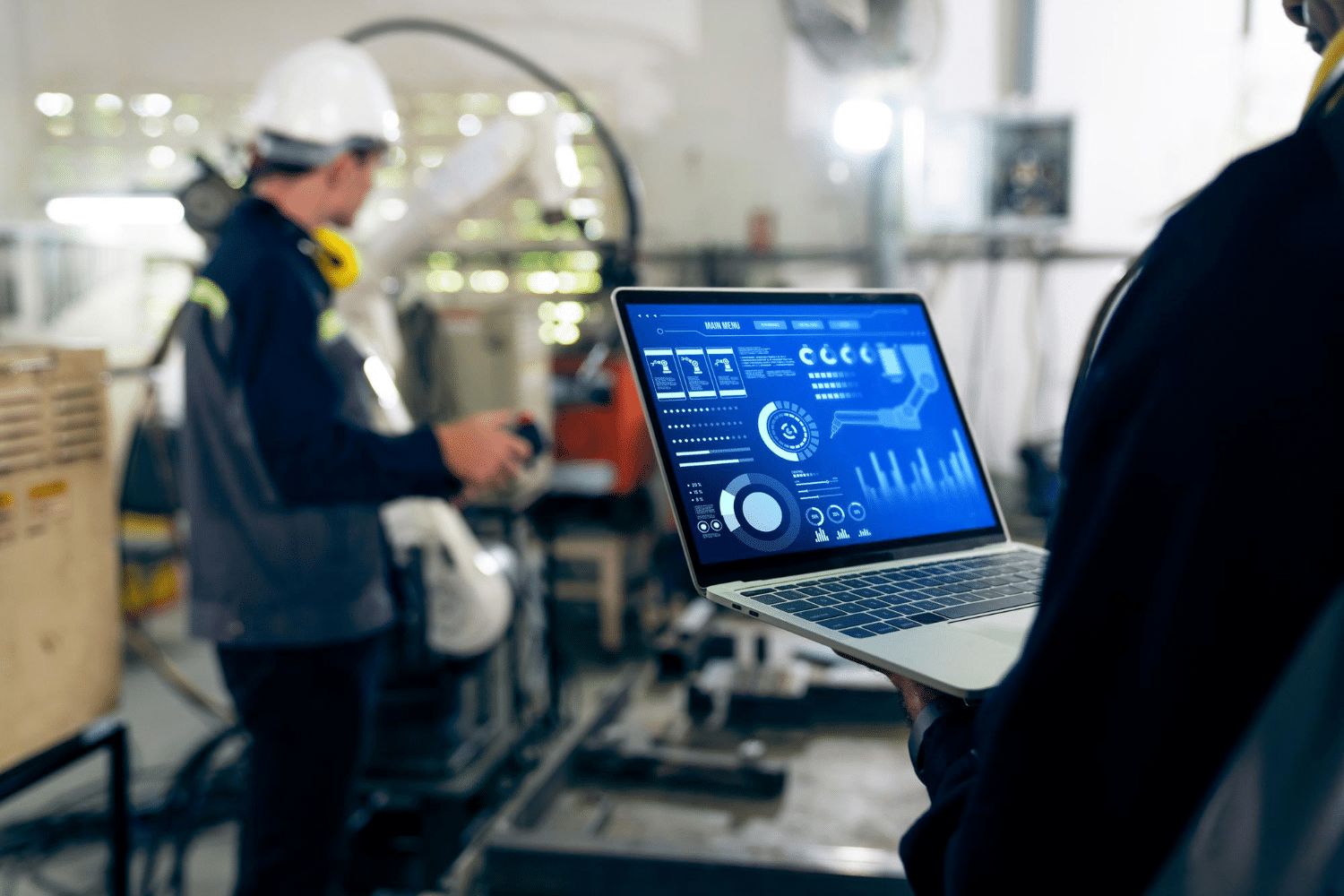
The Crucial Role of Data Analytics in Manufacturing Processes
In the dynamic landscape of modern manufacturing, the profound impact of data analytics cannot be overstated. Often likened to the “new oil,” data has evolved into the lifeblood of efficient, responsive, and agile manufacturing processes. Embracing data analytics is pivotal for manufacturing excellence, influencing key facets of operations.
Informed Decision-Making
Data analytics empowers manufacturers by providing actionable insights, allowing decision-makers to transcend intuition. Real-time data becomes the bedrock for informed, strategic choices, incorporating an understanding of historical trends, market dynamics, and internal performance metrics. This facilitates the optimization of processes for maximum efficiency.
Predictive Maintenance
A game-changer in manufacturing, predictive maintenance leverages data analytics to foresee equipment failures before they occur. Proactive interventions are enabled, minimizing downtime and extending machinery lifespan. Beyond cost savings, this approach ensures a seamless, uninterrupted production flow.
Quality Control and Defect Prevention
Real-time analysis of production data allows for the early detection of anomalies, leading to swift corrective actions. This proactive quality control approach ensures the delivery of high-quality products, simultaneously reducing wastage and rework costs.
Continuous Process Improvement
Data analytics forms the bedrock of continuous improvement initiatives. Through the collection and analysis of performance data, manufacturers identify areas for enhancement, implementing changes incrementally. This iterative approach ensures that processes evolve to meet the ever-changing demands of the market.
Cost Optimization
Analyzing operational data identifies areas where costs can be optimized without compromising quality. This might involve implementing energy-efficient processes, streamlining workflows, or adjusting resource allocations. Data-driven, cost-conscious decisions contribute to the overall financial health and sustainability of the manufacturing operation.
Enhanced Customer Satisfaction
Understanding customer preferences, feedback, and market trends is critical. Data analytics provides insights into customer behavior, enabling manufacturers to tailor products and services to meet evolving expectations. Satisfied customers contribute not only to loyalty but also to positive brand reputation and long-term business success.
Integrate Data Analytics into Manufacturing
1. Define Objectives and Scope
Begin by clearly defining the manufacturing objectives that data analytics will address. This involves understanding the key challenges or inefficiencies in your current processes. Establish a comprehensive scope that outlines the specific areas of manufacturing that analytics will impact. Whether it’s optimizing production, enhancing quality control, or streamlining supply chains, a well-defined objective provides a roadmap for successful implementation.
2. Assess Data Infrastructure
Evaluate the existing data infrastructure within your manufacturing operations. Invest in technologies and systems that can efficiently collect, store, and process large volumes of data. This step ensures that you have a robust foundation, allowing for the seamless integration of analytics tools. The effectiveness of data analytics is heavily dependent on the quality and accessibility of the underlying data.
3. Select Appropriate Tools
Choosing the right analytics tools is crucial for the success of your manufacturing analytics initiative. Consider the complexity of your data and the specific goals you aim to achieve. Basic statistical analysis tools might be suitable for some objectives, while more specialized manufacturing analytics software might be necessary for complex operations. Ensure that the selected tools align with your manufacturing goals and are user-friendly for your team.
This comprehensive approach outlines the crucial steps in integrating data analytics into manufacturing, emphasizing the importance of defining objectives, assessing infrastructure, and selecting appropriate tools.
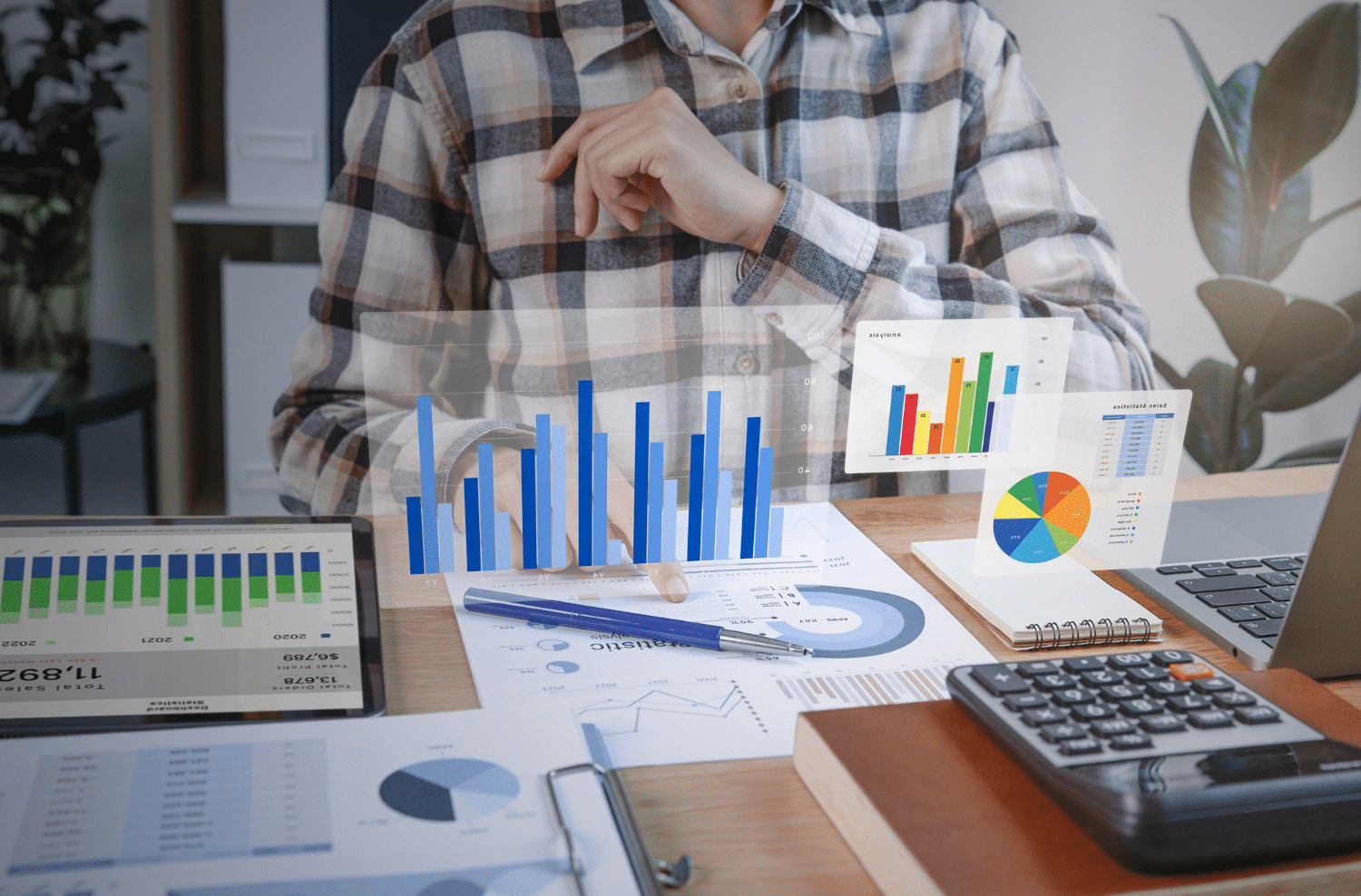
Conclusion: Transforming Manufacturing Through Data Analytics
In manufacturing, its obvious that the integration of data analytics is important. From ancient record-keeping practices to the intricate mechanisms of the Greeks, humanity’s quest for understanding has led us to the sophisticated realm of contemporary data analytics. In the manufacturing sector, where precision and efficiency are paramount, leveraging data becomes not just advantageous but imperative.
The foundations of process improvement, rooted in principles like data analytics, root cause analysis, and the Kaizen philosophy, lay the groundwork for adaptive, efficient, and continuously improving manufacturing processes. Data analytics, acting as a strategic compass, empowers decision-makers to glean actionable insights from historical trends and internal performance metrics.
This journey through time reveals the evolution of data analytics, from statistical analyses in the 17th century to the modern era of big data, the internet, and advanced analytics techniques. The critical role of data analytics in manufacturing processes is underscored by its impact on informed decision-making, predictive maintenance, quality control, continuous process improvement, cost optimization, and enhanced customer satisfaction.
Implementing data analytics in manufacturing involves a systematic approach, which works by clearly defining objectives and scope, evaluating existing data infrastructure, selecting appropriate tools, and implementing strategies. This comprehensive integration positions manufacturers for long-term sustainability and competitiveness.
In conclusion, data analytics is not merely a technological upgrade; it is a strategic imperative reshaping the future of manufacturing. As manufacturing processes become more adaptive, responsive, and intelligent, the profound impact of data analytics continues to unfold, painting a future where efficiency, quality, and innovation converge to define the manufacturing landscape.
Unlock Efficiency with Cadynce
Do you want to leverage your data? Cadynce was made to increase efficiency unify departments, streamline workflows, and gain 360 degree view of your business.
Make the shift towards efficiency without the complexity. Request a call today!